Our Client, based in Doha, QATAR, is seeking qualified staff for their HSE Department. These are all URGENT positions. Closing date is the 31 March 2013. All positions are married / single posts and offer excellent packages with above average tax free salaries, housing, transport and mobiles. Also included in the package is:
Furniture allowance,
Education & Medical up to 4 kids with max age of 18 years old,
Life insurance for employee and medical coverage for his family including 4 kids up to the age of 18 years old,
Economy class ticket for self and dependents of 4 kids with max age of 18 years old,
End of service benefits,
37 working days of annual leave etc.
Preference will be given to Applicants who have worked in QATAR for companies such as Ras Laffan, Dukha or any Oil & Gas project / site. Please note that should you be currently employed in QATAR, you MUST be able to be released from your current Employer. Second preference will be for Applicants who have worked in any GCC country, Far East, Malaysia, Indonesia etc in the Oil & Gas industry.
Basic Function and Scope :
Plans and coordinates a safe and healthy work environment for all Company and contractor’s personnel in the plant. Includes supervising safety staff of 5 professional and technicians, developing and monitoring safety procedures; presenting safety training programs; auditing work practices in assigned area, in particular the “work permit” system; conducting ongoing emergency preparedness program and skills, investigating and advising the HSE Manager on all matters related to incidents or accidents; and preparing appropriate recommendations to prevent their recurrence in the future.
Tasks and Duties:
Supervises and manages staff of five professionals in ongoing Plant HSE program work, including budgeting, managing, shutdown coordination and new construction/start-up. Interacts primarily with senior/mid-level management of Operations, Maintenance and Engineering.
Assists Health, Safety & Environment Manager, the Process Safety Engineer, the Environmental Specialist and Emergency Services Coordinator in the formulation and development of HSE programs in the Plant locations and substitutes as Acting HSE Mgr. on an as required basis. Ensures the availability of safety manuals, hazardous area instruction, safety materials, safety publications and posters, emergency preparedness etc. Brings to the attention of Plant Management unsafe work practices and worksite, and recommends improvements.
Is in charge of the Behavioral Based Safety program implementation. Develops and conducts training programs in safety principles and practices, which include supervising practical exercise. Develops and coordinates orientation programs aimed at promoting accident prevention among personnel, supervises specific emergency drills for personnel in assigned area, and assesses program effectiveness.
Ensures that safety equipment and facilities are kept in the best working condition by developing and initiating preventive maintenance programs and associated procedures; setting up efficient records keeping systems for all equipment under his responsibility and recommends the replacement of faulty equipment.
Oversees the implementation of the “permit to work” system, covering maintenance work and vessel entry procedures. Includes reviewing permits issued by operations personnel, ensuring proper measures are taken prior to commencement of work, such as equipment of plant isolation, shutdowns and that necessary tests (such as gas tests) are taken. Ensures all work area are safe for required work through visits to work sites during dangerous or potentially difficult work.
Participates in incident control during accidents or emergencies in the Plant areas. Investigates incidents and prepares an independent assessment of cause, results and measures to be taken to alleviate future occurrences. Provides leadership for the implementation of the Reporting and Investigation of Incidents and Accidents Procedure and prepares regular reports on injuries sustained in assigned area, and statistical summaries of accidents. Monitors vehicle activity in the plant and recommends action to be taken in cases of unsafe driving practice.
Investigates assigned incidents of environmental pollution, participates in the control of personnel with regard to the awareness and observation of Company safety practices and regulations Maintains incident and investigation records. Analyze trends and develop HSE programs.
May also be requested at the design stage to review safety and engineering aspects of bids to ensure that emergency facilities and equipment and the safety concerns are properly covered.
Inspects new projects construction/installation work on site to ensure that contractor personnel are aware of and carefully observing Company safety practices and regulations.
Ensures that adequate stocks of safety and emergency equipment and protective clothing are available at all times. Prepares requisitions for replenishment of safety materials stock and recommends the purchase of new equipment’s as necessary. Evaluates new items to assess their suitability, reviews related literature and advertising materials and forward recommendations to Manager. Controls the issue and use of such equipment and follows up to replace defective or work clothing and equipment by recommending supply as necessary.
Carries out other similar or related duties such as spot auditing and inspection of work activities in assigned area: maintaining an awareness of developments in his field; carrying out risk assessments, special studies on safety matters; following up on safety training or recommending specialised training requirements for Plant and Safety personnel, and maintaining inspection or activity records and files as required. Responsible for the coordination of periodic checks of the Plant Self Audit Procedure and reporting deficiencies to Management.
Coordinates and reviews safety equipment and procedures for Plant and Field scheduled shutdowns. Includes recruitment of safety personnel where necessary and liaising with Maintenance Planning and Contractors on safety regulations and procedures.
Responsible for the development and support of Company Health, Safety & Environment policies and programs, and carrying out specific duties and responsibilities related to his job as spelled out in Management system documentation, policies, procedures, local documentation, Management System Manual, Safety Manual and other related documents.
Assists in development and support of Company Workplace Health Protection Program, including implementation and administration of regulator fit test program.
Work Contacts:
Regular contracts with operations and maintenance personnel to Management levels to review and follow-up on safe working practices for Plant Operations, and provide advice and assistance as required. Contacts with local police and Government agencies to provide information and/or discuss incidents in the plant and regular contacts with contractor management in relation to Contractor HSE Program, shutdown safety related subjects and specific incident/accident investigations.
Independence of Operation:
Works in accordance with standard procedures and inspection programs and is expected to work independently within these guidelines. Major matters or incidents are referred to Manager for discussion. Work is subject to review and direction by Manager.
Supervisory Responsibility:
Supervises the following:
Safety Supervisor: 1
Safety Officers: 1
Safety Technicians: 3
Minimum Requirements:
• Bachelor’s degree in Engineering or Science discipline or equivalent.
o 12 years’ varied experience in plant HSE matters, including at least 8 years within in petrochemical or oil & gas industry plants environment.
o ISO and OHSAS Lead Auditor (ISO 9001/14000-OHSAS 18001). Familiar with Process Safety Management programs.
o Excellent written and spoken English.
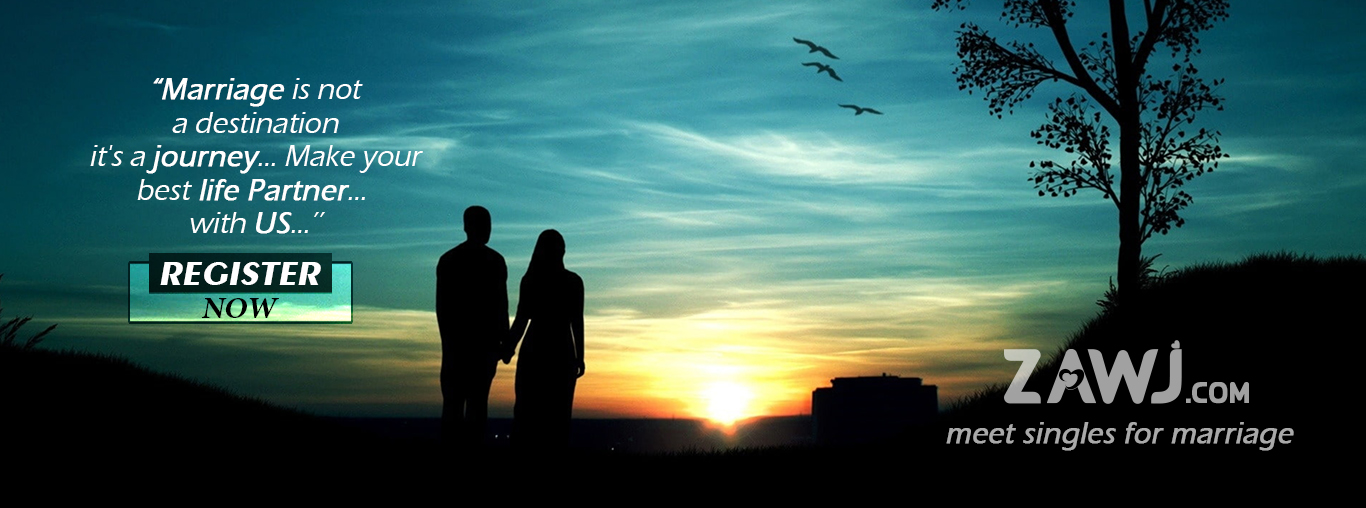
